Onze productieleider wilde gestructureerder gaan werken en altijd een auditwaardige fabriek hebben. Wij als productie wilden dat alle randzaken op dezelfde plek lagen en beschikbaar waren. Dit betreft onder andere stofzuigers, schoonmaakspullen en gereedschap.
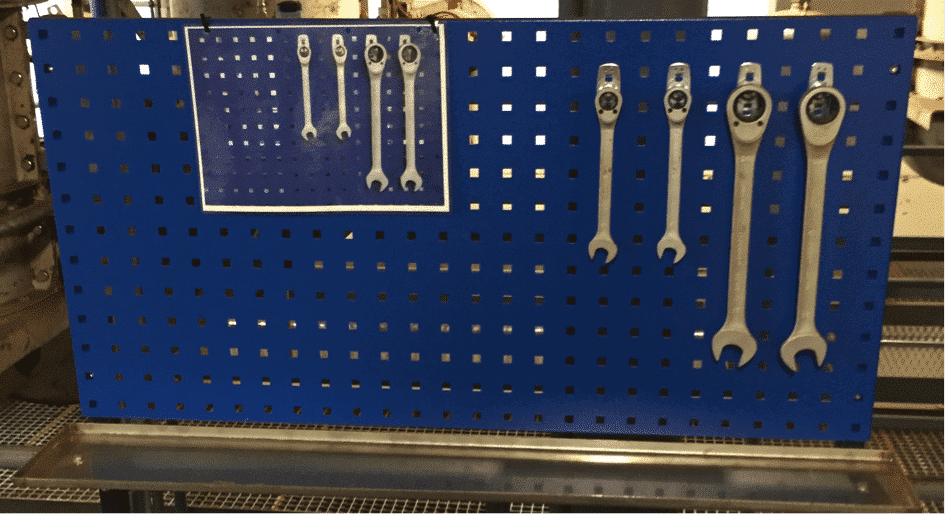
Als er kleine gaatjes ontstaan in de luchtleidingen die het cacaopoeder transporteren, dan kan het voorkomen dat er een kleine hoeveelheid cacaostof vrijkomt in de lucht. Om die reden wordt er tijdens elke dienst schoongemaakt en wordt er elke 8 uur gestofzuigd. Schoonmaakspullen moeten dus makkelijk beschikbaar zijn. We wilden daarom toe naar een gestandaardiseerde manier van werken. Dat je in één oogopslag ziet dat iets anders is dan bedoeld, dat een bezem of stofzuiger niet op z’n plaats staat. Alles heeft namelijk een plaats en alles staat op z’n plaats.
Als iets schoon is, ben je bereid om het schoon te houden
5S Implementatie bij Olam Cocoa
Om te werken aan betere samenwerking tussen collega’s en meer betrokkenheid zijn we bij Olam Cocoa gestart met de implementatie van 5S op de werkvloer. 5S gebeurt op de werkvloer en daarom laten we graag de medewerkers aan het woord die direct te maken hebben gehad met de implementatie van 5S. In een drietal interviews vertellen zijn over hun ervaringen, verbeteringen en de lessen die ze geleerd hebben.
- Vertellen de ploegchefs Rein Rus en Jan Westerveld over hun specifieke ervaringen met het scheiden, het schikken, het schoonmaken, het standaardiseren en het standhouden. Wat hebben ze opgepakt, waar liepen ze tegenaan? Lees hier hun verhaal.
- Laten Richard van Leeuwen (operator) en Michel Schellevis (bouwkundige) vanaf de werkvloer hun licht schijnen op het veranderproces van 5S. Lees het hier.
- Vertelt Mark Wester (production engineer) over de kunst van veranderen en welke lessen je hieruit kan leren. Lees zijn verhaal hier.
Eyeopener
Startpunt was de beleidsbeslissing om 40 leidinggevenden hun Green Belt in Lean te laten behalen. Wij werden kartrekker van het 5S-project (Scheiden, Schikken, Schoonmaken, Standaardiseren en Standhouden), omdat wij als ploegchefs kwaliteitsbewakers zijn en we elkaar goed aanvullen. Wij werken in opvolgende ploegendiensten en kunnen zodoende overlaptijd creëren zonder dat dit veel reistijd kost. Daarnaast was het een mooie kans om meer te leren op zakelijk vlak. De Green Belt training was een eyeopener. Ondanks dat we de werkwijze nog niet kenden, ontdekten we dat we 5S al toepasten (thuis leggen we bijvoorbeeld de messen en vorken apart in de besteklade). Kijkend naar onze uitdaging op de werkvloer was de 5S-methode een logische keuze.
Scheiden
Aan de slag! Eerst opruimen en scheiden. We namen afscheid van een oude rollerbaan die we niet meer gebruikten. Veel reservematerialen hadden we niet nodig, dus deze kregen een enkele reis oud-ijzerbak. Want, voorraad is verlies. Een grote frustratie onder medewerkers was de dagelijkse zoektocht naar de stofzuigerslangen die overal konden liggen. De oplossing was het creëren van specifieke plekken waar altijd voldoende slangen hingen. De slangenhouder hebben we zelf ontworpen!
Schikken
De interne opslag van de fabriek hebben we aan een herschikking onderworpen. Wat staat waar en wat hoort waar? Van werkvoorraden als pallets en emballagemateriaal en hulpmiddelen als een sealapparaat en pompwagens. Door visueel management toe te passen creëerden we overzicht.
Gele lijnen en rode lijnen ter indicatie, plattegronden, het 5S-bord en foto’s van de juiste situatie maken voor iedereen duidelijk wanneer iets wel of niet op z’n plek staat. Daarnaast is visueel management niet alleen handig aan de buitenkant, maar ook de gelopen audits en de verbeteringen kunnen beter worden gemanaged. Visueel management is echt een manier om beter, slimmer, effectievere en efficiënter te werken.
Aanvankelijk vonden medewerkers het wat kinderachtig, maar toch gingen steeds meer afdelingen onze acties kopiëren. Geen verspilde uren meer voor het zoeken naar materialen en het beheersen van de voorraad is veel effectiever.
Standaardiseren
We zijn nu bezig met het standaardiseren van de werkomgeving en de processen. Zo hebben we binnen een deel van het proces alle boutjes vervangen door boutjes van dezelfde maat. Een ander voorbeeld van standaardisatie betreft de maalschijven om cacaokoek tot poeder te malen: de pennenplaten. Het wisselen van die platen leverde om de haverklap stilstand op. We hebben nu ingepland om standaard na 21 dagen alle platen te wisselen. Door deze standaardisatie is de effectiviteit van de machine verhoogd in de week van de maalschijvenwissel.
Standhouden en schoon houden
Standhouden is heel waardevol, maar tegelijkertijd lastig, omdat mensen vaak geprikkeld willen worden door nieuwe dingen en verbeteringen. Aan de andere kant is het ook zo dat als iets eenmaal schoon is, mensen eerder bereid zijn om het schoon te houden. Ons motto is: de standaard van vandaag is de slechtste van morgen! Hierdoor verbeteren we die standaard dagelijks.
Het standhouden doen we door middel van audits. Dit houdt in dat elke ploeg twee keer per maand een ronde loopt volgens een schema met een aantal vast controlepunten. Een van de operators die aanvankelijk erg negatief was, heeft het audit-schema persoonlijk opgesteld. Hij loopt nu voorop! In de toekomst hopen we dit schema af te kunnen schaffen, omdat we in een oogopslag afwijkingen kunnen zien.
Klein beginnen
Toen we begonnen met het 5S-project riepen veel medewerkers: “We beginnen weer met iets en dat maken we vast weer niet af! Wanneer wordt er eens iets aan ons operators gevraagd?” We hebben toen een kernteam opgericht met daar omheen vijf satelliet teams, bestaande uit operators. Door die structuur wilden we meer continuïteit en draagvlak creëren. Ieder team pakte een deel van de fabriek aan: het is veel leuker en effectiever om klein te beginnen. Door het klein te houden zien mensen veel eerder hun eigen resultaat. Dat motiveert enorm! Om richting aan de verbeteringen te geven, hebben we als kernteam een prioriteitenmatrix gemaakt en er vervolgens voor gekozen om met zo weinig mogelijk middelen zo veel mogelijk te bereiken.
Lean is een hele mooie denkwijze en 5S ligt nu veel dichter bij de mensen!
De winst
Kijkend naar de situatie ‘voor’ en de situatie ‘na’, zien we een groot verschil. Als je een willekeurige operator vraagt wat hij van de huidige situatie vindt, dan zegt hij: “Fijn die vaste plek voor de stofzuiger en die gele lijnen rondom de trappen!” Naar schatting scheelt het toepassen van visueel management ongeveer 10 procent tijd per dienst. De schoonmaakacties die we voorheen 3 keer per jaar met 10 man deden, doen we nu met minder mensen in kortere tijd. Als voedingsproducent is het belangrijk dat de omgeving waar het gemaakt wordt voedselveilig is. Dat is een voorwaarde voor ons en voor onze klanten. We hebben ongeveer één keer per maand klanten over de vloer en ze zijn allemaal te spreken over de poederfabriek!
Als er nu een probleem ontstaat, denken we op een andere manier na over de oplossing. De operator denkt mee en neemt eigen initiatief. Er wordt overlegd met de ploegleiding en werkwijzen worden gedeeld. We zijn erachter gekomen dat we zaken wel moeten blijven benoemen en discussies niet uit de weg moeten gaan. Het is geen standaard dagelijks werk: we zijn uren kwijtgeraakt om mensen te overtuigen dat dit de beste weg was.
We gaan de werkwijze en denkwijze nu ook op de andere afdelingen introduceren.
Meer weten over de implementatie van 5S?
5S is onmisbaar binnen een continu verbeterende organisatie. Alle elementen van continu verbeteren zitten verweven in de methodiek en 5S is onderdeel van het Lean huis. Door iedere dag te sturen op 5S werkt een organisatie aan het in de praktijk brengen van continu verbeteren.
Wil je meer weten over 5S, de implementatie van 5S of het gebruik van RPA hierbij? Neem dan contact met ons op via 020 – 345 3015 of contact@upd.nl.